New nanotech fiber: Robust handling, shocking performance
Rice University's latest nanotechnology breakthrough was more
than 10 years in the making, but it still came with a shock. Scientists from
Rice, the Dutch firm Teijin Aramid, the U.S. Air Force and Israel's Technion
Institute this week unveiled a new carbon nanotube (CNT) fiber that looks and
acts like textile thread and conducts electricity and heat like a metal wire.
In this week's issue of Science, the researchers describe an
industrially scalable process for making the threadlike fibers, which
outperform commercially available high-performance materials in a number of
ways. "We finally have a nanotube fiber with properties that don't exist
in any other material," said lead researcher Matteo Pasquali, professor of
chemical and biomolecular engineering and chemistry at Rice. "It looks
like black cotton thread but behaves like both metal wires and strong carbon
fibers."
The
research team includes academic, government and industrial scientists from
Rice; Teijin Aramid's headquarters in Arnhem, the Netherlands; the
Technion-Israel Institute of Technology in Haifa, Israel; and the Air Force
Research Laboratory (AFRL) in Dayton, Ohio.
"The
new CNT fibers have a thermal conductivity approaching that of the best
graphite fibers but with 10 times greater electrical conductivity," said
study co-author Marcin Otto, business development manager at Teijin Aramid.
"Graphite fibers are also brittle, while the new CNT fibers are as
flexible and tough as a textile thread. We expect this combination of
properties will lead to new products with unique capabilities for the
aerospace, automotive, medical and smart-clothing markets."
The
phenomenal properties of carbon nanotubes have enthralled scientists from the
moment of their discovery in 1991. The hollow tubes of pure carbon, which are
nearly as wide as a strand of DNA, are about 100 times stronger than steel at
one-sixth the weight. Nanotubes' conductive properties -- for both electricity
and heat -- rival the best metal conductors. They also can serve as
light-activated semiconductors, drug-delivery devices and even sponges to soak
up oil.
Unfortunately,
carbon nanotubes are also the prima donna of nanomaterials; they are difficult
to work with, despite their exquisite potential. For starters, finding the
means to produce bulk quantities of nanotubes took almost a decade. Scientists
also learned early on that there were several dozen types of nanotubes -- each
with unique material and electrical properties; and engineers have yet to find
a way to produce just one type. Instead, all production methods yield a
hodgepodge of types, often in hairball-like clumps.
Creating
large-scale objects from these clumps of nanotubes has been a challenge. A
threadlike fiber that is less than one-quarter the thickness of a human hair
will contain tens of millions of nanotubes packed side by side. Ideally, these
nanotubes will be perfectly aligned -- like pencils in a box -- and tightly
packed. Some labs have explored means of growing such fibers whole, but the
production rates for these "solid-state" fibers have proven quite
slow compared with fiber-production methods that rely on a chemical process
called "wet spinning." In this process, clumps of raw nanotubes are
dissolved in a liquid and squirted through tiny holes to form long strands.
Shortly
after arriving at Rice in 2000, Pasquali began studying CNT wet-spinning
methods with the late Richard Smalley, a nanotechnology pioneer and the
namesake of Rice's Smalley Institute for Nanoscale Science and Technology. In
2003, two years before his untimely death, Smalley worked with Pasquali and
colleagues to create the first pure nanotube fibers. The work established an
industrially relevant wet-spinning process for nanotubes that was analogous to
the methods used to create high-performance aramid fibers -- like Teijin's
Twaron -- which are used in bulletproof vests and other products. But the
process needed to be refined. The fibers weren't very strong or conductive, due
partly to gaps and misalignment of the millions of nanotubes inside them.
"Achieving
very high packing and alignment of the carbon nanotubes in the fibers is
critical," said study co-author Yeshayahu Talmon, director of Technion's
Russell Berrie Nanotechnology Institute, who began collaborating with Pasquali
about five years ago.
The
next big breakthrough came in 2009, when Talmon, Pasquali and colleagues
discovered the first true solvent for nanotubes -- chlorosulfonic acid. For the
first time, scientists had a way to create highly concentrated solutions of
nanotubes, a development that led to improved alignment and packing.
"Until
that time, no one thought that spinning out of chlorosulfonic acid was possible
because it reacts with water," Pasquali said. "A graduate student in
my lab, Natnael Bahabtu, found simple ways to show that CNT fibers could be
spun from chlorosulfonic acid solutions. That was critical for this new
process."
Pasquali
said other labs had found that the strength and conductivity of spun fibers
could also be improved if the starting material -- the clumps of raw nanotubes
-- contained long nanotubes with few atomic defects. In 2010, Pasquali and
Talmon began experimenting with nanotubes from different suppliers and working
with AFRL scientists to measure the precise electrical and thermal properties
of the improved fibers.
During
the same period, Otto was evaluating methods that different research centers
had proposed for making CNT fibers. He envisaged combining Pasquali's
discoveries, Teijin Aramid's know-how and the use of long CNTs to further the
development of high performance CNT fibers. In 2010, Teijin Aramid set up and
funded a project with Rice, and the company's fiber-spinning experts have
collaborated with Rice scientists throughout the project.
"The
Teijin scientific and technical help led to immediate improvements in strength
and conductivity," Pasquali said.
Study
co-author Junichiro Kono, a Rice professor of electrical and computer
engineering, said, "The research showed that the electrical conductivity
of the fibers could be tuned and optimized with techniques that were applied
after initial production. This led to the highest conductivity ever reported
for a macroscopic CNT fiber."
The fibers reported in Science have about 10 times the tensile strength
and electrical and thermal conductivity of the best previously reported
wet-spun CNT fibers, Pasquali said. The specific electrical conductivity of the
new fibers is on par with copper, gold and aluminum wires, but the new material
has advantages over metal wires.
For
example, one application where high strength and electrical conductivity could
prove useful would be in data and low-power applications, Pasquali said.
"Metal
wires will break in rollers and other production machinery if they are too
thin," he said. "In many cases, people use metal wires that are far
more thick than required for the electrical needs, simply because it's not
feasible to produce a thinner wire. Data cables are a particularly good example
of this."
Source: Rice
University
Leave Your Comments!
Share What’s Going on
in your brain about the Topic. We need Your Response . Feel free to leave comments!
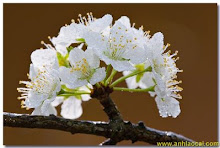